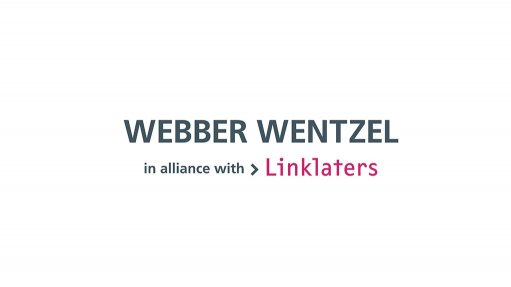
Current logistical bottlenecks present high risks for contractors in completing capital projects, for miners and other industries, and they need to protect themselves against penalties
Supply chain disruptions, which emerged as a result of Covid-19 lockdowns in 2020, and were joined by rising inflation towards the end of 2021, have intensified in the first part of 2022. With the war in Ukraine and the Covid-19 shutdown in Shanghai, it looks as if disruptions may worsen.
The other side of logistical disruption and the war in Ukraine is that it is causing a spike in the prices of certain commodities, so mining companies are more anxious than ever to accelerate expansion projects – even as their contractors are battling to secure the necessary inputs.
For example, the shortage of microchips, which are used in a vast range of consumer products, including cell phones and automotive vehicles, stemmed not only from the closure of factories but also rising demand for technology, when more employees had to work from home. Three-quarters of microchip production is located in East Asia, according to the New York Times.
Another area of acute shortage over the past two years has been steel, as not only were mills shut during Covid-19 but, when they re-started, they underestimated the extent of economic recovery. This has caused a spike in the cost of certain steel products.
The costs and timelines for importing goods have increased dramatically, with a 500% increase in the freight costs of using a 12-meter container to send goods by sea from China to South Africa.
Additionally, Covid-19 cases continue to affect the outputs of suppliers, manufacturers and contractors at various levels of the supply chain. For example, an outbreak of Covid-19 at a supplier or sub-supplier compromises its capacity to complete production timeously, which in turn delays delivery to manufacturers and contractors.
These delays and heightened costs are causing contractors and OEMs to seek ways to manage risks and disclaim responsibility for time and cost overruns on large capital projects. Material Adverse Event or Force Majeure clauses may not assist, as the materiality threshold may not be met in respect of the former and supply chain disruption is unlikely to be construed as an unforeseen or unavoidable event in relation to the latter.
With no immediate prospect of this problem being resolved, contractors that need to procure critical capital items reliant on inputs like steel, microchips or the logistics chain are having to consider including additional clauses in their contracts to protect themselves from the ramifications of failing to deliver within anticipated timelines. Contractors need to acknowledge that there are higher levels of commercial risk and manage these differently.
Where there are concerns that a potential delay in the supply chain will have an unintentional knock-on effect on the construction period, the time for completion and the defects date (and these delays are not attributable to the contractor), the contractor may consider including back-to-back provisions in their contracts with suppliers in order to mitigate these risks. In addition to providing for contractual relief, contractors should reduce their reliance on a single critical source of supply and look for alternatives. Sourcing products closer to home or using local products may also alleviate risk.
The knock-on effect of risk to corporate reputation should be considered when selecting a supplier and the relevant geopolitical risk ought to form part of this evaluation. Sustainability of supply may form an important part of ESG reporting for contractors too.
Written by Tyron Theessen and Megan Jarvis, Partners at Webber Wentzel